Two years of disruption have caused thousands of firms everywhere to remain short of staff. But things may be finally looking up for manufacturers.
Today, fundamental shifts in the labor market driven primarily by technology adoption create fresh opportunities for workers to step into new roles. Completely new skills will, however, be required to navigate this dynamic and evolving labor market.
Author Teodora Gaici | Copperberg
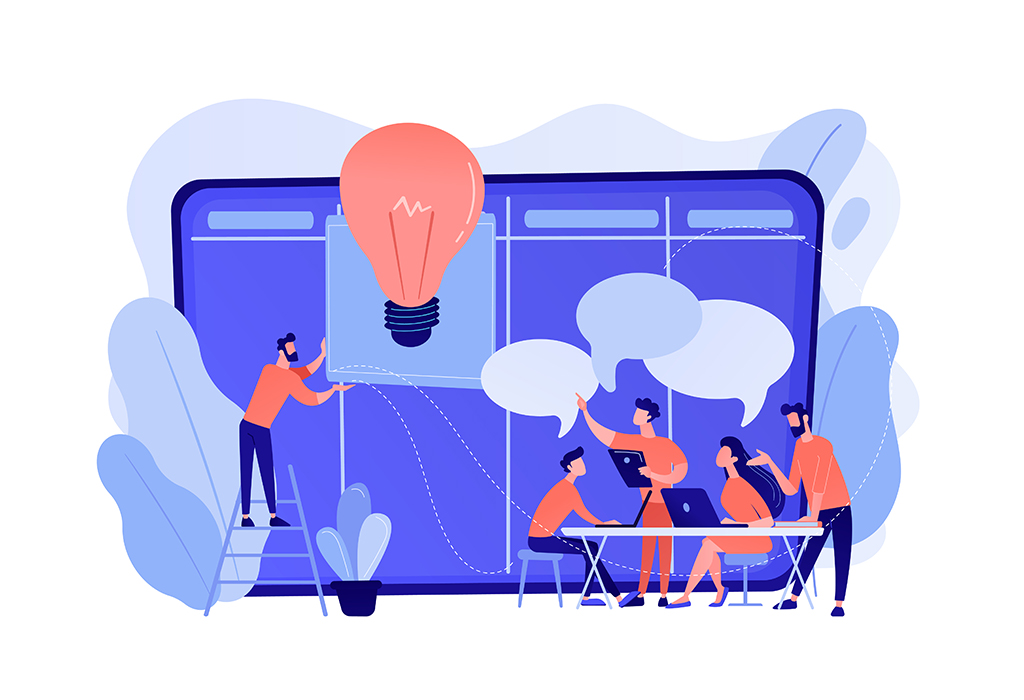
Photo: Freepik
Millions of workers who labor in manufacturing were vulnerable to shifts in working patterns over the past two years. To survive a crisis like COVID-19, industrial firms have had to act rapidly to move beyond tried-and-tested practices and implement alternative working arrangements. The International Labor Organization estimates that “almost 560 million people were working from home in 2020 during the height of the pandemic.” Many of the rest chose to operate on a hybrid schedule. But the quick transition from in-person to fully remote or hybrid work has not been an easy feat for all industrial workers. As more work moved online, older adults with low levels of digital skills have stepped out of the workforce much earlier than originally planned. Understaffed firms struggled to fill positions with skilled workers thenceforth as, according to statistics, “nearly 500,000 jobs have remained open in manufacturing” in the last months.
But the workplace, as industrial firms used to know it, no longer exists. Notwithstanding the widening digital skills gap leaving many jobs unfilled, manufacturers presently continue their venture into new technology-driven work environments. Some, however, plan to upskill and reskill existing team members for new roles to confront the shortage of capable workers.
Things are certainly improving. An industry-leading analysis from The Information Technology and Innovation Foundation confirms that the present labor disruption is no longer a catastrophic threat but a strategic driver of growth that leads to technological innovation:
“Disruption is often a driver of growth, as companies adopting more efficient technologies and new business models gain market share. Therefore, policymakers should not try to slow down labor disruption; if anything, they should try to speed it up, especially by supporting technological innovation.” — The Information Technology and Innovation Foundation, Even After COVID-19, the U.S. Labor Market Remains More Stable Than People Think
The future of manufacturing work is brimming with opportunities thanks to the rise of technology. Almost overnight, advances in technology have begun to reshape the global manufacturing labor market at a brisk tempo, driving demand for new roles and skills. Here are some of the most in-demand roles and the new skills required for workers to move into such positions to address the currently overwhelming talent shortages within manufacturing.
The Age of Technology Transforms Manufacturing Work at a Record Pace
A major shift of roles and skills is now underway in the global manufacturing labor market. The adoption of new technology is leading to a significant rise in the need for:
- Data Scientists
Modern manufacturing runs on data. Time and again, firms gather big volumes of unruly and disparate data yet have no clear understanding of how to shape it into usable forms or generate value from it. This is where the role of data scientists steps in. A data scientist with technical, mathematical, and statistical knowledge will clean, organize, blend, and enrich large chunks of data for powerful insights used to forecast outcomes, make intelligent decisions, and solve complex problems.
The demand for data scientists will continue to rise as more firms come to recognize the indispensability of such experts to manufacturing work. The U.S. Bureau of Labor Statistics projects a growth of 31.4% in data science occupations through 2030—listing data science careers among the top 30 fastest-growing in the 2020–30 decade.
- Collaborative Robot Specialists
Interest in working next to robots is flourishing across the manufacturing industry. A report anticipates the global collaborative robots market will grow at a CAGR of 42.0% to reach $11,684.7 million by 2027.
The potential is unlimited for industrial workers who join forces with robots. But the increased presence of collaborative robots in manufacturing facilities drives demand for experts with specialized knowledge about how and where to use such machinery systems for improvements in operations. Manufacturers need specialists who can implement controlled mechanisms to improve the operational capabilities of robots, balance tasks between workers and robots, and ensure safe cooperation at work sites.
- Solution Architects
The past two years have been a big test for manufacturers. As industrial firms sought to digitize and adapt to new working environments, some have grappled with a fundamental disconnect between business focus and technology innovation. This is why hiring for solution architect roles is on the rise.
Working with a solution architect plays an increasingly integral part in the process of introducing new technology solutions into a firm. After a thorough analysis of the manufacturer’s business and technical requirements, such experts identify suitable technology solutions to address specific needs and problems and determine how the new technology fits into the existing IT infrastructure. Taking direction from solution architects will foster a stronger alignment between the business and IT and help manufacturers make sound technology decisions.
Those who move fast in replacing legacy roles and redeploying industrial workers to new ways of working will pave the way for manufacturers to prosper in today’s new era of transformation.
Modern Manufacturing Roles Give Rise to a Whole New Set of Essential Skills
As the global labor market rebounds, industrial workers must figure out how to pick up skills for the new roles created. Workers must be, now more than ever, exceptionally skilled at:
- Analyzing large sets of data and interpreting results
- Thinking analytically and critically
- Solving complex problems quickly and creatively
- Programming and controlling robots
- Using advanced digital technology
- Operating industrial machinery and equipment
- Communicating effectively with internal teams and customers
- Embedding a culture of continuous improvement and innovation
Now, the manufacturing labor market is shifting more firmly in favor of hybrid work models. But the world of manufacturing work will continue to evolve in the coming years. As work patterns change, so will the skills required of industrial workers.