Data is the commodity that fuels modern-day manufacturing.
The uptick in industrial innovation, from real time inventory management to remote machine monitoring, is inherently centered around data.
As manufacturers gather impressive amounts of information from different sources and mine it for powerful insights into equipment performance, product quality, or supply chain visibility, a rigorous data integration environment is an underlying necessity.
Author Teodora Gaici | Copperberg
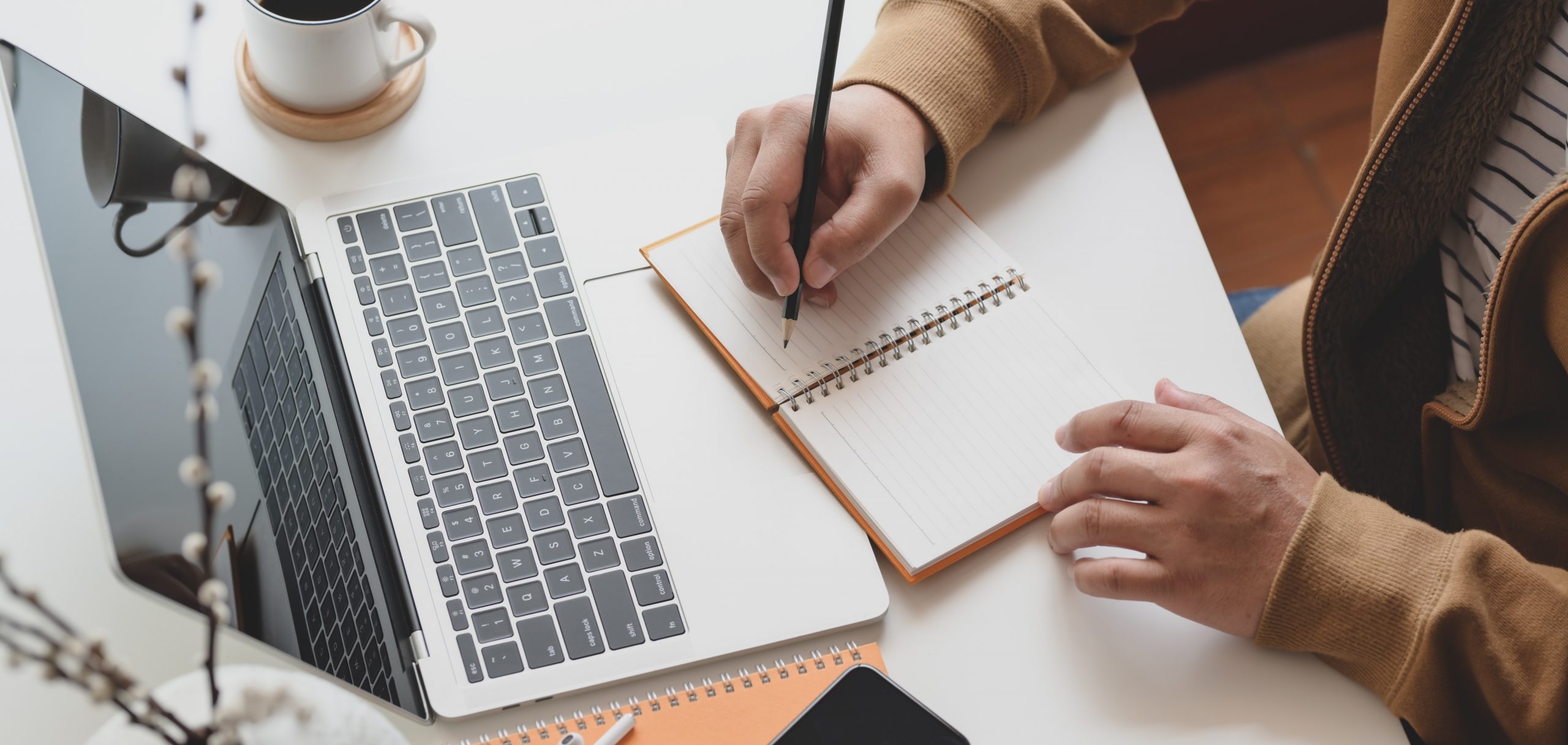
A constant stream of timely information is presumably the engine of manufacturing growth. Admittedly, immense swaths of data that capture machine-level information are poised to optimize field operations, prevent unscheduled downtime, and yield superior demand forecasts.
But the mere amount of data is not necessarily an indicator of intelligent manufacturing processes—a high level of data usability is.
Any given dataset is deemed valuable only if it’s useful, manageable, and actionable. When the attention is diverted away from these rigorous standards, low-quality information may lead to faulty assumptions and, as a result, bring manufacturing operations to an abrupt halt.
Amid rising data quality-related concerns, manufacturers process and share a daily tangle of information across multiple systems or applications. There is, however, a fairly robust link that can unify all this continuously-acquired data to help professionals extract more value from it.
That link is called data integration.
A well-defined integration strategy is an invaluable asset to any company. Not only it allows manufacturers to filter out inaccuracies from their existing data points, but it also makes information manageable enough to power decision-making.
All production activities, from the procurement of raw materials to the physical creation, can be directly supported by the use of integrated, consistent, and high-quality information. With that in mind, is integrated data just razor-thin evidence of superior production outcomes? Or a long-term endeavor that seamlessly aids you in capturing and resolving recurring data issues to maximize manufacturing efficiency?
In many cases, integrating heterogeneous data throughout a manufacturing organization is particularly challenging due to the multidisciplinary nature of the industry itself, remote synchronization, or (seemingly) trivial logistics issues. But exchanging unstructured information across systems is largely inadvisable as poor-quality data can swiftly impede production and overall manufacturing growth.
Crumbling Under the Weight of Data
Data naturally comes in varied formats and is inevitably extracted from diverse sources. Any distributed dataset offers significant performance gains or, alternatively, is part of a bigger problem: erroneous decision-making.
As pressures for product and service quality improvement repeatedly pile up in the manufacturing sector, a data-informed standpoint that is accurate, precise, and valid reigns supreme over aimless assumptions. Yet the lack of a heedful data integration strategy gives rise to arbitrary guesswork.
How?
Typically, spurious decisions are based on inconsistent information that comes from:
ᐅ Incomplete records.
Critical information may be missing from your database due to a human data entry error or an unexpected system shutdown.
Whether specific values are absent (e.g., the name of a supplier or his geographical coverage in a specific region) or the entire database has been instantly wiped out, manufacturers should take immediate action to ensure data completeness—a particularly important aspect to improving information usability.
ᐅ Duplicate data streams.
Transferring data from one system to another might unwittingly multiply unique files—partially or completely.
Suppose the duplicated record accurately displays the name of a particular supplier and pinpoints his geographical coverage. His contact information, however, is not identical, and both files exhibit a different phone number.
Misleading supplier tracking information might automatically hinder manufacturing productivity, hamper deliverability, and ultimately, lead to lost business.
ᐅ Data silos.
Achieving optimal supply chain visibility requires superior datasets. The same premise holds true for quality control; better data, better quality management.
Too often, the valuable data that manufacturers need resides in disparate systems. Trouble is, siloed data not only inhibits quality assurance but also disrupts distribution, cripples supply chain management, and restrains reporting accuracy.
Combing through disconnected data is also especially time-consuming and may significantly slow down production planning.
There’s no warranty that manufacturers are immune to the rash decisions that result from imprecise information. The consequences are costly and, at times, translate into production chaos due to quality or delivery bottlenecks.
Product quality is not interchangeable; neither is consistent, clear-cut, and readily available information that facilitates manufacturing intelligence to prevent overproduction, conduct in-progress production adjustments, and enable on-time delivery.
Harmony Brings Wealth
The integration of data is paramount to frictionless operations, systematic gains in forecasting accuracy, and excellent service.
Closing the gaps in data integration allows for superior inventory management, and makes optimized supply chain planning faster. Similarly, a well-architected plan supports supply chain automation, which, in turn, increases production reliability to help manufacturers rise on top of the competition.
Now that multiple systems monitor production line vitals or oversee maintenance activities for manufacturing equipment, data integration is a company-wide undertaking. Removing volatile data and integrating critical information from siloed applications can bring underperforming equipment to light. This way, manufacturers can prevent possible disruptions that (if not properly addressed!) may lead to losses in market share or reputation.
Fragmented data can be a minefield or… a goldmine—if that information is properly consolidated.
Every piece of data that is fully integrated across the organization spurs innovation and greater manufacturing agility. From the factory floor to the customer, professionals can make data-driven decisions to invest in advanced technologies that reduce labor costs, accelerate production cycles, and create new revenue streams.
Integrate to Innovate
Data truly is an organizational asset… if ruling out contradictory information and integrating the entire data ecosystem across each line of business is a top priority for professionals.
Manufacturers that bring together diverse data points and fuse their best characteristics into useful insights could shorten time-to-value.
The benefits, however, don’t stop at the shop floor.
Integrating incompatible data formats from divergent sources deepens line-of-business visibility to rapidly improve decision-making and establish leaner manufacturing processes.
In other words, fostering a uniform data-centric company culture is the key to gaining a significant competitive edge in a fast-paced industry.
Drill down on accurate, real time, and consistent data records that empower manufacturers to achieve operational excellence, take customer responsiveness to greater heights, and expand into new markets.