Digitalization, the all-powerful architect of Industry 5.0, is accelerating manufacturing’s evolutionary leap. Those who settle into the new reality of increased human-machine collaboration achieve breakthrough innovations with unerring precision. Without manual processes that perpetually chip away at their productivity, digital-native manufacturers can increase their organization’s readiness to change, speed up turnarounds, and minimize production expenses while reducing waste.
Realizing the true potential of technology-aided manufacturing is an interdependent act that largely hinges on expertise. Going above and beyond the digitalization of manufacturing will allow professionals to facilitate the spread of know-how across their organization to establish a more responsive working environment, ensure lean production, and improve factory uptime.
Author Teodora Gaici | Copperberg
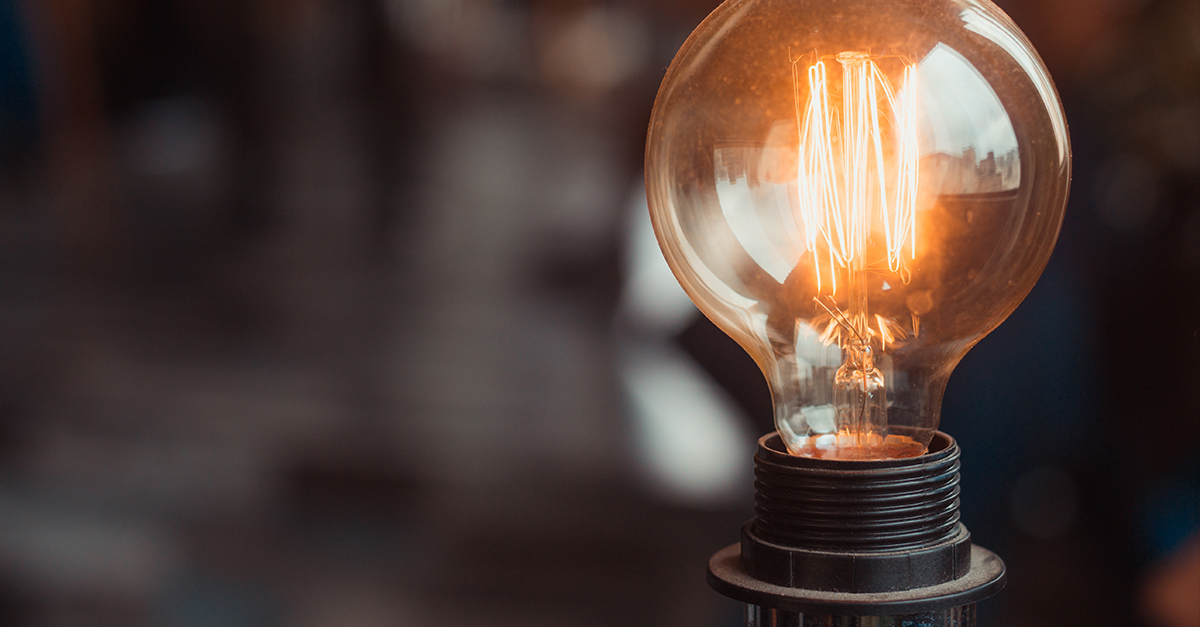
Years ago, human-powered machines set the course of the manufacturing industry in a direction that firmly valued human craftsmanship. Since such devices would require little maintenance, they were functionally feasible, economically viable, and above all, socially desirable. Even unskilled workers could deliver good-quality products as long as they were putting out enough physical effort.
Those days are long gone.
Over time, the demand for individualized products has continuously soared, and mass production took an inevitable back seat in certain industries. Human craftsmanship still matters. But to meet custom-tailored client requirements at a rapid pace, modern-day manufacturers need advanced data, knowledge, and digital literacy—not rigid skill sets.
Now that impressive volumes of information must be effectively formatted, analyzed, and interpreted, a digitized infrastructure is an imminent necessity for enriching practical knowledge—namely, your know-how—to properly deliver on the promised value.
Know-how is a much-talked-about concept with large implications in the manufacturing sector. Simply put, it’s a set of procedures or technical skills acquired through a process of “learning, reasoning with analogies, and intuition.” It might be seen as an ironclad ability, but know-how is more than hands-on expertise typically related to general manufacturing processes or machinery. To correctly assess and improve organizational-level performance, manufacturers need both:
- Practical know-how—the expertise that is acquired by experience and allows manufacturers to efficiently execute on their objectives.
- Contextual know-how—the norms and implicit values generally shared within an organization.
An environment that innately strengthens know-how while promoting expertise exchange may exponentially reduce waiting times. It can also help manufacturers react to (or even predict!) consumer demand more efficiently and drive rapid product innovations without sacrificing quality.
In a highly industrialized world that is increasingly defined by speed, how can professionals widely diffuse know-how—faster and consistently? It all begins with a well-defined digitalization strategy.
When Digital Technology Meets Manufacturing
The industry is rife with technological advancements that are readily blurring the lines between physical and digital spaces. With the advent of the following technological forces that underpin physical operations, professionals can prolifically drive smart manufacturing processes and develop a shared organizational vision.
1 – Cognitive digital twins.
The digital twin, or the virtual representation of a specific physical entity that precisely predicts how a product will ultimately function, naturally contains three segments:
- The physical product in real space.
- The virtual product in virtual space.
- The connections that tie the virtual and real products together.
This dynamic digital simulation of a real-world factory, production line, or any other object happens in real time and is powered by data—a combination that promptly anticipates faulty product design, reduces operating costs, and enriches organizational competitiveness.
A cognitive digital twin brings something even greater to the table: autonomous manufacturing. Although a conscious virtual twin can process thought, acquire input knowledge, and resolve impending loopholes by itself, stimulating human-machine interactions will yield superior results, including better machine efficiency and operation safety.
More than facilitating immersive human-machine connections, routing possible device failures, and lowering power consumption, cognitive systems enable professionals to better understand and control industrial processes. Digital twins will factor in historical data to continuously expand the virtual replica of the product based on past performance. Through context-specific insights, manufacturers can enlarge, manage, and exploit rich knowledge structures. They can also customize this practical information to specific individuals and noticeably fuel expertise sharing.
The ability to capitalize on all these knowledge-based skills will empower manufacturers to make strategic decisions at the organizational level, prove their expertise, and collaborate more efficiently throughout the different phases of a product’s life cycle.
2 – Virtual reality technology.
As virtual reality (VR) has sparked interest worldwide, traditional manufacturing training lost ground to real time learning.
The widespread use of VR technology among professionals has already transformed worker safety and manufacturing skills training. Unlike static instructor-led training programs, VR applications immerse the user in a simulated computer environment and allow this individual to directly manipulate objects.
Through interactive environments, manufacturers execute specific actions, which, consequently, will support experiential learning—a process that enables the mind to store information subconsciously and consciously.
Any production process that is simulated digitally may reveal inefficiencies and potentially dangerous assembly line procedures. VR technology facilitates the quick spread of data while enabling manufacturers to send and receive crucial information across the entire network.
Interactive learning environments also encourage evaluative attitudes and empower professionals to learn by doing. As a result, VR-enhanced training is the manufacturer’s ally in the permanent quest towards cutting out waste and enriching operational efficiency. Hands-on activities, when done collaboratively, may eliminate unnecessary processes and swiftly power up lean production schemes.
The end result? A group of well-informed manufacturers that work together to develop high-quality products and fasten time-to-market.
The Rise of the Collective Mindset
Digitalization is a beacon for the path ahead in manufacturing. While professionals are just a few clicks away from the factory of the future, conventional facilities are increasingly being nullified.
Technology is fundamentally transforming how products are designed, fabricated, tested, or serviced. The lack of a shared mindset, however, may render any technological investment worthless.
Manufacturers must collectively ramp up efforts to promote know-how throughout the organization. Otherwise, the company-wide digitalization strategy might fall short and put the brakes on the production line.
Knowledge sharing is an invaluable activity that revolves around the entire manufacturing process, from production to distribution. Increasing the rate of information exchange through digital-based manufacturing will most likely enable professionals to respond to rapid market change and deliver timely products at the highest quality.