This year’s field service trends have vastly accelerated technology adoption in the wake of the COVID-19 pandemic. The potential exists, but it is often at odds with the way in which industry players expect to realize the promised ROI of field service technology.
Author Teodora Gaici | Copperberg
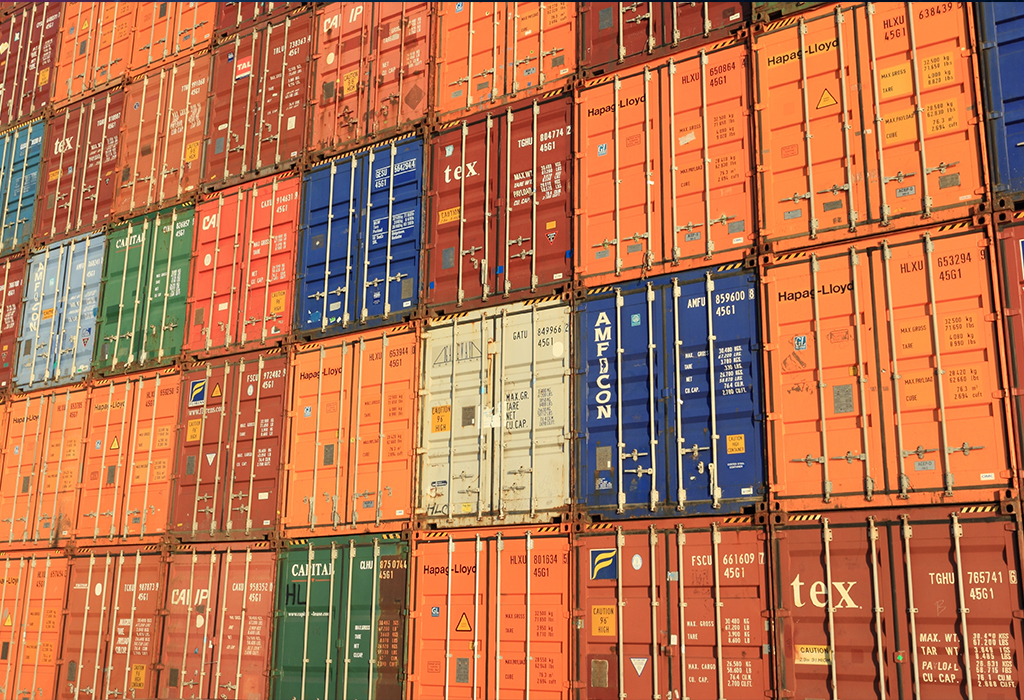
What foils the promissory aspects of today’s field service technology trends?
The popularity of digitalization and servitization is, among other trends, shaping field service investments. Firms are scrambling to acquire new technology, but many of them fail to achieve the expected ROI of their investments.
Frequently, the overriding assumption is that technology itself is at fault. Yet the real issue behind the lack of investment gains is inefficient parts planning — an issue traditional firms have been less inclined to resolve.
To realize the true benefits of field service technology, industry leaders need to prepare for the challenge of technician-held inventory by implementing a well-rounded change management plan.
Michael Ross, Director of Product Strategy at Baxter Planning — a renowned leader in parts planning for field service operations — touches upon this subject in his Field Service Trends session, held as part of Copperberg’s 2020 Field Service US Summit.
With insights largely derived from Michael Ross’s presentation, this article will look at the current trends in field service technology, how they impact a firm’s stocking strategy for service parts, and why parts planning is key to solving the problem of unrealized gains.
Today’s Field Service Trends Are Putting Firms on a Speedy Path to Technology Adoption
The field service industry has seen an influx of trends that are spurring up technology investments. From digitalization and servitization to route optimization and predictive analytics, all of these voguish concepts have captured the attention of many industry players. “Some of these trends are real and they have already begun to shape how field service is done,” says Michael Ross “[and] many of these trends are quite interrelated, as well.”
One of the intertwined trends making headlines in recent years is the idea of technician retirement. A wide-ranging skills gap expectedly appears when an experienced technician retires — a gap that is sometimes seen as not being thoroughly aided by technology. Michael Ross acknowledges this issue by noting that:
“Directly or indirectly, many of [today’s field service] trends deal with that overarching trend of turnover, loss of skills, and difficulty in providing information to the replacements that don’t have those decades of experience.”
Yet all this time, the problem with technician retirement has been a rather mulish act of resistance to change; technician turnover briskly expedites technology adoption and in turn, machines make it increasingly easier for years of technical intelligence to be passed on to other field service workers. As revealed in the Field Service Trends presentation, industry players take on new technology and field service trends to precisely minimize the skills gap; here’s how:
- Route Optimization Tools allow workers to do more calls per day, helping firms to get more productivity out of their technician workforce.
- Digitalization and Electronic Training Systems enable firms to bridge the skills gap by helping them to move down the path of servitization.
- Artificial Intelligence Technology collects essential information — including service call history and customer experience records — and makes it available to the next generation of technicians to help predict the best service intervention when necessary.
That is just to name a few of the field service trends that are currently spawning innovation by not only promising shrunken skill gaps but also:
- Improved technician productivity
- Faster troubleshooting
- Smarter equipment
- Higher first-time fix
Experts are seeing the value of these trends beyond all the hype. What is, then, the problem with achieving it? Michael Ross is careful to distinguish the issue as he explains that:
“Many of these trends have profound impacts on parts planning needs, [and] companies that recognize the intertwined impact of these trends on parts planning are more likely to get the expected ROI benefits of their technology investments.”
The Parts Issue Remains As Industry Players Take on New Field Service Trends and Technology
Unknowingly or not, many firms have a parts planning issue. The problem with the lack of ROI is not the extent of the technology’s potential in terms of knowledge dissemination, but the technician’s inability to cast traditional strategies aside when turning to a technology-enabled approach. Technicians may wisely use technology to spread information and knowledge about parts throughout the firm — and then, succumb to parts hoarding instead of actively managing their inventory. Michael Ross shares a telling story about parts stocking gone wrong:
“Historically, technicians had the experience to determine their own stock lists: they had knowledge of products and knew how customers used — or perhaps misused — the product that they were servicing. [But] almost all of them carried too many parts.”
Today, this example of technician-held inventory serves as a reminder of how to not do business. At the end of the day, “you still need to have the right parts, in the right place, at the right time to achieve the promised benefits of all these new technologies,” outlines Michael Ross. Technician-held inventory only accentuates the stigma surrounding traditional planning approaches, which also often assume that technicians will simply adjust to new technology. They won’t.
The role of this year’s field service trends in addressing the critical parts planning challenge is of interest to multiple organizations, but many are still tempted to leave their parts stocking process ‘as-is.’ That is not the way to do it. As exemplified in the Field Service Trends session, change management is essentially important in adopting a new technology trend — and parts planning for field service should be proactive, not reactive.
Technician-Held Inventory Is Risky Behavior, Signaling Firms to Switch to Active Parts Planning
As firms adopt any new field service technology associated with today’s most-touted trends, they need to plan for a proactive change management approach. This strategy should primarily address the impact of new technology on the firm’s technician workforce and its parts stocking.
In short, this means that it is predominantly vital for service leaders to actively manage the technological impact on the firm’s parts planning needs to rapidly readjust their go-to strategy if an issue that hampers ROI is detected.
For additional information on why active parts planning is critical for ROI success with new field service trends, be sure to view Michael Ross’s Field Service Trends presentation at this year’s Field Service US Summit, now available on demand.