In the first quarter of 2020, the COVID-19 outbreak was declared a global pandemic by the World Health Organization. To date, the pandemic cost the global economy $10 trillion, a cost that is forecasted to increase to $12.5 trillion through 2024.
Author Radiana Pit | Copperberg
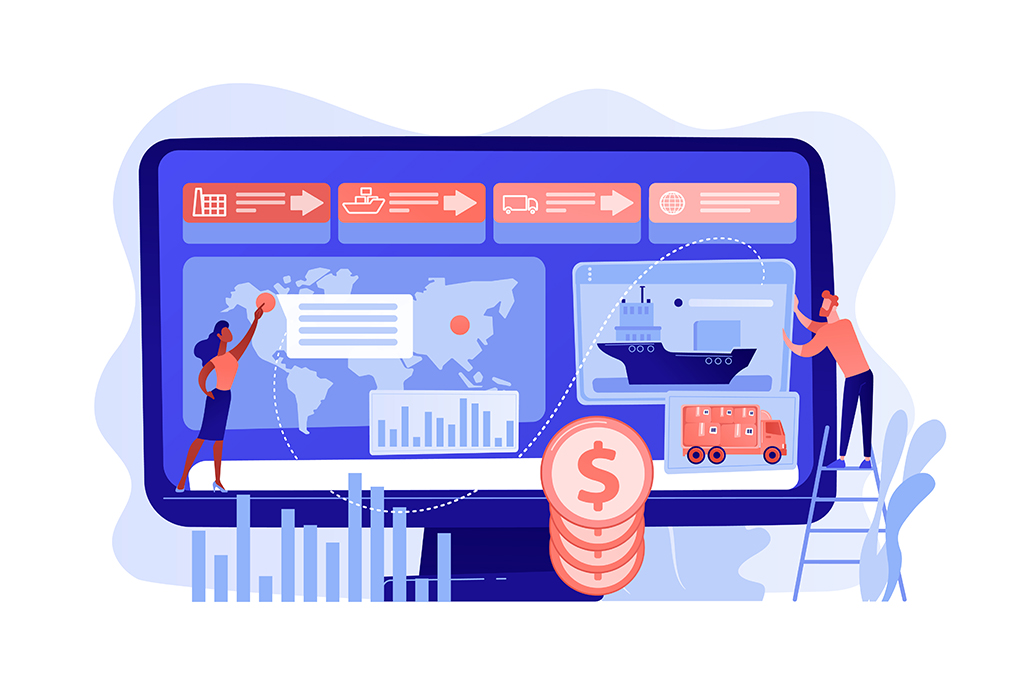
Photo: Freepik
The crisis exposed vulnerabilities in international supply chains that became even weaker as the following events took place:
-
The provisional Brexit deal or The EU – UK Trade and Cooperation Agreement (TCA) that became effective on January 1, 2021, an event that imposed a new border operating model, creating trade flow uncertainties between the UK and the EU.
-
The bizarre Suez Canal situation on March 23, 2021, when Ever Given, a giant container ship, become lodged sideways in the Suez Canal due to high winds and low visibility from an Egyptian sandstorm, blocking the world’s busiest corridor for six days and freezing $40 billion worth of trade.
Now, the eruption of the Hunga Tonga-Hunga Haʻapai submarine volcano on January 15, 2022— which is likely the largest eruption of the 21st century to date—caused devastating tsunamis in Fiji, New Zealand, Japan, Peru, and more, reminding the world of the 2010 eruption of the Eyjafjallajokull volcano in Iceland responsible for the worst flight disruption over Europe since the Second World War, with a loss of $1.7 billion in over an eight-day period.
Furthermore, concerns regarding global networks are heightened as the supply chain disruption from the conflict between Russia and Ukraine threatens to negatively impact commodity prices and supply availability, firm-level export controls and sanctions, private-sector cybersecurity, and wider geopolitical stability.
All things considered, business leaders are beginning to understand the importance of creating contingency plans for worst-case scenarios and are increasingly focused on building resilience within their supply chains. By drawing from past events, they can learn valuable lessons about how to efficiently predict, endure, and recover from large-scale disruptions both at the present and in the future.
Lesson #1: Supply chain digitization
The impact of the COVID-19 pandemic on global supply chains has led to capacity issues, a 300% surge in freight costs, and the supply chain digital transformation boom. The latter phenomenon has been driven by the rise of Big Data and analytics, artificial intelligence (AI), augmented reality (AR), and other advanced technology that promises to optimize supply chain operations by reducing inefficiencies, lowering costs, and enhancing flexibility.
The need for supply chain flexibility has become even more pressing during the Suez Canal emergency, which proved that resilience and agility are critical even for scenarios that have nothing to do with the pandemic. Beyond the pandemic, there will always be ongoing risks to global networks that need to be considered at all times for more informed supply chain management.
Digitization creates an opportunity to futureproof supply chain management, providing indispensable tools for total network visibility, from demand to inventory and capacity. It also provides tools for increased domestic production, such as 3D printing, which minimizes dependency on international supply chains, high inventory costs, and asset downtime.
Machine learning and artificial intelligence can also be harnessed for predictive and prescriptive analytics to develop model risk scenarios and preprogrammed responses, thus increasing responsiveness and accelerating reaction times when incidents occur.
From the impressive list of digital tools critical to supply chain resiliency, blockchain also stands out as a solution for parts supply stability, supplier collaboration, data management, information systems, and visibility. Beyond optimizing the supply chain, blockchain also provides the ability to verify authenticity and detect counterfeit spare parts, thus lowering the risk of sourcing illicit products.
Lesson #2: Supply chain security threats
The digital transformation of global supply chains comes with many benefits, including enhanced connectivity and network visibility, but it also increases the risk of cyber incidents. According to research by Deloitte, there has been a surge in cyber threats amid the COVID-19 pandemic and these threats will only multiply in a digital-first world.
The nation-state attack on the SolarWinds network management system in December 2020 is a compelling example regarding the importance of supply chain security. The breach was one of the biggest incidents in recent years, affecting over 18,000 organizations, including the Pentagon and the Department of Homeland Security.
But beyond preventing security breaches, supply chain security management must also include considerations for data protection, data locality, fraud prevention, data governance, and third-party risk.
With post-Brexit GDPR and more foreseeable changes in the threat and regulatory environments for cybersecurity and data privacy, global suppliers need to find optimal ways to maintain compliance while also collecting, storing, and managing data for informed decision making. As such, addressing vulnerabilities in supply chain cybersecurity is critical, with risk mitigation, penetration testing, and data encryption being top priorities in the process of securing data movement.
Lesson #3: Options for multi-sourcing
Up to 90% of supply chain decision-makers have reported that they’ve experienced a direct business impact from souring issues, which were aggravated by the COVID-19 pandemic. For single-sourced OEMs, a global pandemic can have a catastrophic impact. But multi-sourcing provides a solution for business continuity in times of crisis.
By diversifying the network and collaborating with multiple suppliers, OEMs can develop flexibility and contain the risk of supply chain disruptions. However, this adds complexity to the supply chain that can be managed with the help of automation and software solutions that provide total visibility into the supply network.
Another key consideration is that multi-sourcing can also cause friction between suppliers and increase competitiveness. But the risks of multi-sourcing as a solution to build resilience far outweigh the benefits. In case of natural disasters or a global pandemic when one or more of the source vendors are prevented from delivering their goods, OEMs with access to multiple sources can still have a chance to acquire the materials they need for their production.
Lesson #4: Opportunity for geographic diversity
When the pandemic started in China, which is considered the world’s factory, global supply chains were dramatically affected. To prepare for another scenario in which production is halted by the inability of a primary vendor in one location to deliver the expected goods, OEMs are exploring sourcing options in geographic areas they’ve never considered before.
Regions like Mexico, Malaysia, and Vietnam have become of high interest among companies looking to diversity their supplier networks and global footprint. By diversifying their networks, OEMs are not only multi-sourcing but also nearshoring, meaning that they devise localized solutions within their networks for greater supply chain resiliency.
Likewise, partnering with local distributors and leveraging their skills and distribution network can decrease the risk of failed deliveries by global distributors that are overwhelmed by the unprecedented demand created by COVID-19 and the events that followed it.
Lesson #5: Flexible inventory and transportation approach
Distributing goods from a single distribution or storage unit has become a risky approach considering the supply chain vulnerabilities exposed by the pandemic, natural disasters, and other disruptive occurrences like the Suez Canal blockage.
Today, having all inventory in one place can negatively impact a business if the site is either shut down or too far away from a destination that might be challenging to reach due to restrictions or environmental threats. As such, distributing inventory across multiple locations closer to their targets can help industry players expand their geographical reach, reduce shipping costs, increase shipping and fulfillment rates, and minimize warehousing costs.
Beyond inventory flexibility, planning logistics and transportation with flexibility in mind is key. In the case of natural disasters, global pandemic restrictions, or situations such as the one at the Suez Canal, alternatives in logistics and transportation are essential. So, leveraging technology to plan for different types of scenarios and mapping out multiple route options can help restore supply chain resilience.
Becoming agile, responsive, and resilient
Supply chain disruptions are not new to industry players. OEMs and suppliers around the globe have long known that disturbances, such as material scarcity, price fluctuation, transportation delays, and cyber attacks that may interrupt their activities or processes are part of the business. Yet, before 2020, not many prepared for worst-case scenarios such as global pandemics or natural disasters.
From the COVID-19 outbreak to the bizarre Suez Canal crisis and now the conflict between Russia and Ukraine, industry leaders have learned to expect the unexpected. With proper analysis, planning, and execution, they will gain the ability to accelerate reaction time and adapt to the changes ahead.
The next supply chain disruption is always just around the corner. As risks continue to flare up, OEMs and suppliers that want to endure and recover from incoming disturbances know that achieving resiliency means reducing dependencies on individual suppliers in low-cost regions, devising inventory optimization strategies, increasing supply chain visibility, and investing in digital tools that can streamline those processes.