The advent of the Fourth Industrial Revolution has changed the business landscape and will continue to do so for a long time. Today, the increased use of artificial intelligence (AI), cloud computing, 3D printing, robotics, the Internet of Things (IoT), and advanced wireless technologies continues to fuse the digital, biological, and physical worlds, ushering in a new economic era.
Author Radiana Pit | Copperberg
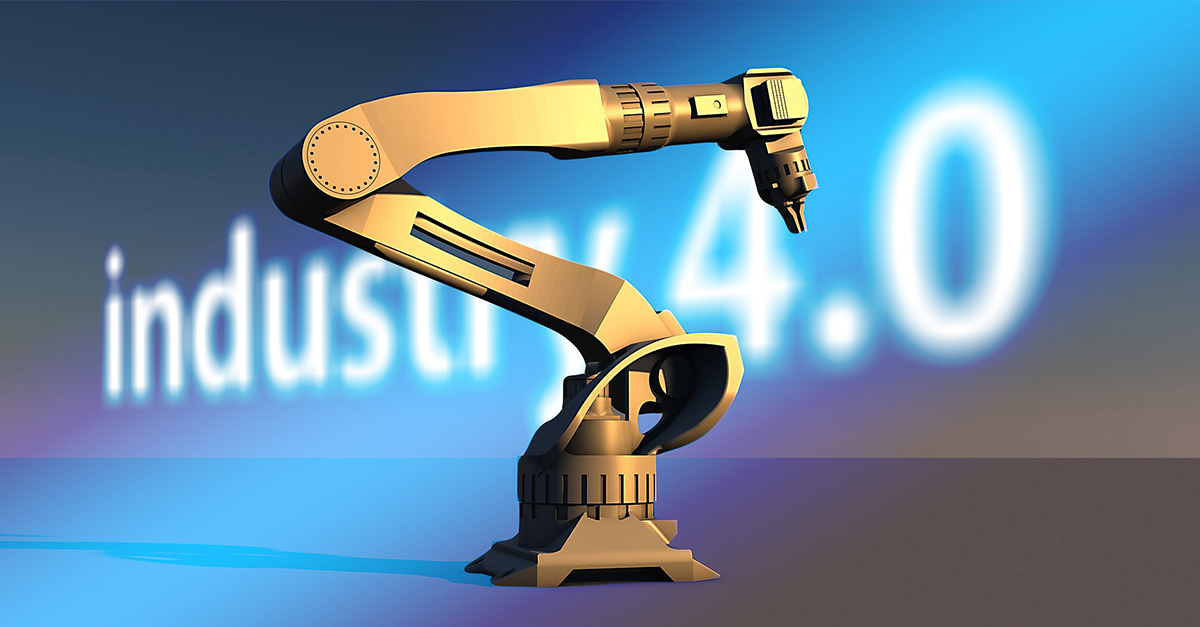
The question is: can your manufacturing business keep up with the pace of change? As long as your informational technology (IT) and operational technology (OT) play nicely together, the answer is a resounding yes.
What is the cost of falling behind?
Although your legacy systems are essential for your day-to-day operations, they might be based on outdated technologies. So, why exactly is it so important to update them as long as they do their job?
Because, otherwise, your systems can crash anytime due to their increasing number of software support issues and security vulnerabilities. This can easily result in costly downtime that can negatively impact production capacity, customer experience, company morale, and more. And today, when the competition is fiercer than ever, downtime often translates to long-lasting crippling effects on business outcomes.
Yet some legacy systems and machines are hard to replace, especially those you use for core business processes such as high-volume data processing. Unfortunately, at some point, these technologies won’t be able to keep up anymore, and you will have to upgrade them. And it’s better to do so sooner than later.
You will definitely gain a competitive advantage.
The manufacturing industry is dominated by antiquated technologies. But, by bringing IT and OT together, you have a chance to outperform your competitors with lightweight solutions, accelerate digital transformation, and also:
- Make your clients and employees happier with sleek UIs and intuitive, user-centric experiences.
- Prepare your business for the future with modern solutions that ensure your business is agile enough to evolve and expand.
- Unlock big data opportunities that will allow you to make more informed decisions and quality checks.
- Improve performance and reliability by reducing outage risks and preventing related losses.
And the best part is that you can benefit from all of the above without having to throw away your existing equipment.
Extend the life of your legacy systems and machines.
Although most legacy systems can’t fully support innovation or compliance, the equipment on your production floor can be IoT-compatible. This means that you can easily adopt an Industrial IoT (IIoT) framework to connect and synchronize some of your devices and machines through software tools and platforms that were specifically created to support your core operations with minimal human intervention.
So, consider the following tools as your gateway to the digital era:
- Smart sensors: By deploying IIoT sensors, you can complete your data set at a low cost. You can attach these sensors to your legacy machines to provide connected feedback and detect factors such as vibration and temperature.
- Video cameras: Higher resolution cameras are cheaper and smaller than ever, making it easier for you to monitor analog gauges, supervise worker location, and capture remote equipment status.
- Device servers: This technology is not only easy to install and mount, but it also allows you to connect legacy equipment to modern industrial computers and translate protocols from several devices. When it comes to your legacy equipment, device servers can do wonders for interconnectivity with modern networks.
These cost-effective solutions will help simplify your architecture and prepare you to adapt, refresh, and integrate easier. New and old technologies will always have to work together, so why not simply align your existing equipment with the modern models that were created to augment—and not replace—the essential components in your infrastructure?
Extending the life of your old equipment with modern solutions is one of the key steps in closing the gap between IT and OT. By implementing tools such as smart sensors, you can connect your legacy and analog equipment, thus creating a single, centralized network of systems and devices. And this centralized network is the key to gaining real-time visibility into your operations for a more thorough understanding of your manufacturing processes and more informed decision-making.
Prioritize cooperation and security.
Being mindful of potential security issues is vital if you want to create a connected factory and future-proof your business.
While your IT team (or partner) may be accustomed to advanced security solutions, your OT department might be lacking in modern defenses. So, when going through your IT/OT convergence, it’s important to establish solid security policies for identifying and mitigating cyber threats, human errors, and technical vulnerabilities.
For this, your IT and OT teams will have to collaborate closely, conduct regular risk assessments, and devise a holistic incident detection and response strategy. According to the Center for Internet Security (CIS), there are six basic security controls that can help your IT/OT teams get started on the right foot:
- Inventory and control of hardware assets
- Inventory and control of software assets
- Continuous vulnerability management
- Controlled use of administrative privileges
- Secure configurations for hardware and software computers
- Audit logs maintenance, monitoring, and analysis
Consider these best practices to facilitate dialogue between your teams and ensure that your modernization plan can run its course safely without being exposed to security risks.
Are you ready to become the factory of the future?
The factory of the future is smart and connected. And this statement doesn’t only refer to intelligent devices and centralized networks, but also to new ways of thinking that will emerge from the collision of IT and OT in the context of IIoT.
It surely sounds like a future most manufacturers would want to be a part of. Luckily, you can get one step ahead of your industry peers by extending the life of your IoT-compatible equipment rather than replacing it and by connecting the silos that separate your IT and OT environments.
This will give you a solid foundation for constant integration with current and future technologies that can make your business more productive and profitable in the digital era.