The digital twin concept has been around since 2002 when it was publicly introduced as a model underlying product lifecycle management (PLM). It has come a long way since then thanks to the evolution of the Industrial Internet of Things (IIoT) — which enables true connectivity between physical components and their digital counterparts.
Author Radiana Pit | Copperberg
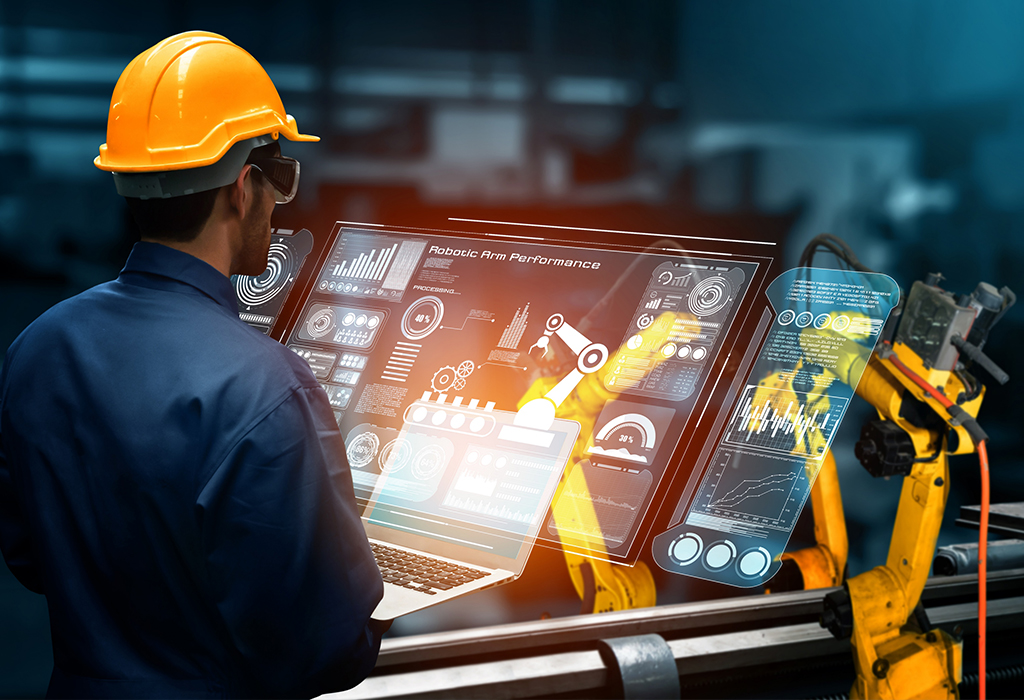
In 2017, Gartner predicted that by 2021, “half of the large industrial companies will use digital twins, resulting in those organizations gaining a 10% improvement in effectiveness.”
Of course, back then, no one took into account the unforeseeable impact of 2020’s COVID-19 pandemic, which forced the industry to take a closer look at this promising technology and accelerate adoption.
What is a digital twin and how does it work?
A digital twin is a virtual model or digital replica of a system, process, product, or service that is connected to its physical counterpart through sensors that generate real-time data. By integrating advanced technology such as artificial intelligence (AI), machine learning (ML), and software analytics with spatial network graphs, digital twins create simulation models that are in constant sync and alignment with their physical counterparts. Using ML capabilities, digital twins continuously learn and update themselves using multiple sources in order to provide an accurate near real-time status.
Industrial organizations that use digital twins can gather a great deal of information about the operations of their physical systems. Digital twins can capture environmental data such as location, configuration, or services records, and ultimately provide insights into everything from design and historical operations to predictive servicing. In fact, you can use digital twins to achieve a series of objectives, including:
- Optimizing the operation and maintenance of physical assets and manufacturing processes;
- Gaining real-time visibility into products in use;
- Connecting disparate systems and promoting traceability with a digital thread;
- Monitoring and troubleshooting equipment remotely;
- Simulating a variety of what-if scenarios through virtual tests;
- Predicting equipment behavior in different environments, conditions, and situations;
- Reducing development costs and improving the reliability of a product by using digital twins in the design phase;
- Clarifying equipment specifications with suppliers and optimizing the final design for manufacturing;
- Validating quality by comparing the final product with its digital twin;
- Collecting performance data and generating usage insights;
- Experimenting with new data without halting production or sacrificing safety;
- Refining processes virtually before implementation;
- Training new employees and reducing the impact of human errors on the physical system;
- Preventing downtime by analyzing data and monitoring systems.
Considering the potential of digital twins, major software and industrial companies have included digital twins in their 2018 portfolios. Back then, Thomas Kaiser, SAP Senior Vice President of IoT, said that: “Digital twins are becoming a business imperative, covering the entire lifecycle of an asset or process and forming the foundation for connected products and services. Companies that fail to respond will be left behind.”
But what’s the status of digital twins now? How have they performed in 2020 and what role will they play in the new normal?
The accelerated adoption of digital twins
In the Spring of 2020, the digital twins of smart cities became critical tools that helped governments determine their next policy steps. Before the outbreak, digital twins were already considered for disaster management, but the pandemic was the catalyst that highlighted the importance of extending these solutions.
And the same is true for the industrial sector. Although in the past couple of years digital twins have garnered more attention from manufacturers and the world at large, the events this year have accelerated adoption.
In a world remodeled by COVID-19, manufacturing and supply chains must become even more efficient to meet consumer demands. And, luckily, achieving the next level of efficiency is possible thanks to digital twins. Companies that implement this technology can not only digitally replicate and analyze their entire manufacturing footprint, but they can also use it to prepare for sudden shortages of raw materials and identify secondary supply sources while also taking into account costs, service, and capacity. This can ensure continuous uptime and lead to cost savings.
Undoubtedly, the value of digital twins will continue to increase. According to Juniper Research’s report on digital twins in IoT, investments in digital twin technology will increase by 17% in 2021, reaching $12.7 billion.
And this is only natural since digital twins can enhance safety and resilience, which are becoming top priorities in the world of business. Additionally, digital twins are not as expensive to implement as they used to be. Thanks to the emergence of increasingly favorable storage and computing costs, businesses can now adopt this technology and apply it to a variety of use cases in order to drive greater business value.
Conclusion
By improving product design and engineering, enhancing equipment performance, creating digital records of raw materials or serialized parts, and reducing overall production costs, a digital twin can add real value to your business. It can also help you identify revenue growth opportunities by pinpointing which products are ready for upgrades.
But, more importantly, a digital twin enables you to streamline your operations and answer key strategic questions in times like these, when economic volatility and uncertainty rule over the industry.
In 2021 and beyond, digital twin adoption is expected to reach new heights and, to stay ahead of the competition, you should consider diving deeper into this promising technology and adding it to your digital transformation initiatives. Doing so will prepare you for next-generation use cases that are based on simulations, AI, and computer vision applications.
Although the new normal is still a work in progress, one thing is clear: the business landscape is becoming increasingly digital and the world at large is operating more virtually. The best thing you can do is to seize the opportunity created by the convergence between the physical and digital worlds and devise a digital twin strategy that will set you up for future success.